FOR EVERY PRODUCTION THE RIGHT ONE
Annealing
Annealing is the treatment of a workpiece at a certain temperature, with a certain holding time and subsequent cooling adapted to achieve the desired material properties.
Important annealing treatments:
- normal anneling
- stress relief anneling
- soft annealing
- spheroidizing (GKZ annealing)
- large-grain annealing
- recrystallization annealing
- solution annealing
Adequate Systherms furnaces for this process:
Hardening is a heat treatment consisting of austenitising and cooling under such conditions that an increase in hardness occurs through more or less complete transformation of the austenite, usually into martensite. Austenitising is the treatment step in which the workpiece is brought to austenitising temperature and the matrix of the steel becomes austenitic through complete phase transformation and carbide dissolution. Cooling takes place after austenitising. For the entire workpiece to assume a martensitic structure, the rate of temperature drop must be greater than the critical cooling rate of the respective steel. Cooling can take place in various media, which differ characteristically in their cooling effect in the various temperature ranges.
Adequate Systherms furnaces for this treatment:
Hardening
Tempering
Tempering follows immediately after the hardening process. Only the combination of hardening + tempering (= quenching and tempering) produces the quenched and tempered structure with the optimised mechanical properties for the respective application. Like hardening, tempering is one of the thermal processes that influence the mechanical properties of the entire component, i.e. from the peripheral zone to the core areas. The purpose of tempering is to reduce the hardness of a hardened component to such an extent that the required toughness values are achieved. The simultaneous loss of hardness is accepted. The choice of atmosphere influences the surface of the components.
Suitable Systherms – furnaces for these treatments:
Case hardening is one of the thermochemical processes. In this process, the surface layer of components and tools is carburised with a carbon-emitting medium and then quenched. This improves the mechanical properties of the component edge layer. The quenching can take place either directly from the carburising temperature or after intermediate cooling and reheating to a material-specific hardening temperature. These are only two variants of possible temperature-time sequences during case hardening. Carburisation is usually carried out between 880 and 980 (1050)°C. After hardening the carburised components, tempering is mainly required to reduce the stresses resulting from hardening and to set the required service strengths. For case hardening, the heat treaters have various plant technologies at their disposal, such as low-pressure plants.
Adequate Systherms – furnaces for this treatment:
Case hardening
Nitriding
Nitriding is a thermochemical treatment in which the surfaces of the workpieces are enriched with nitrogen. This causes an increase in surface hardness through the formation of nitrides. In nitrocarburising, carbon is added in addition to nitrogen. The process is used for low-alloy and unalloyed materials and is suitable for workpieces that have been machined to finished size. By enriching the surface layer with nitrogen or nitrogen and carbon, the strength behaviour under static and dynamic stress, the wear behaviour and the corrosion behaviour are improved.
Adequate Systherms – furnaces for this treatment:
Hardness and wear resistance essentially determine the service life of tools. In addition, dimensional accuracy and low residual stress are indispensable prerequisites for perfect functioning of many tools. Structural changes, such as a transformation of residual austenite during use, can lead to tool rejection; they should therefore be avoided as far as possible. Especially when using high-alloy tool steels, the retained austenite content of a steel can have a decisive influence on its usability and quality. The targeted conversion of retained austenite by combining conventional heat treatment techniques with deep-freezing is often the technically and economically most sensible method of achieving the desired material properties.
Adequate Systherms – furnace for this treatment:
- horizontal tempering furnaces, direct heated type VAD
Freezing
Soldering
Soldering is a thermal process for joining materials, whereby a liquid phase is formed by melting a solder (fusion soldering) or by diffusion at the interfaces (diffusion soldering). A surface alloy is produced, but the workpiece is not melted in depth: The liquidus temperature of the base materials is not reached. After the solder has solidified, a material-locking connection is produced, as in welding.
Adequate Systherms – furnaces for this treatment:
Sintering is a process for the production or modification of (working) materials. In this process, fine-grained ceramic or metallic materials are heated, often under increased pressure, but the temperatures remain below the melting temperature of the main components, so that the shape of the workpiece is retained. This usually results in shrinkage because the particles of the starting material become denser and pore spaces are filled up. A basic distinction is made between solid phase sintering and liquid phase sintering, in which a melt is also produced. Sintering processes are of great importance in ceramics production („sintered glass ceramics“) and in metallurgy („sintered metals“ and „powder metallurgy“). Through the temperature treatment of sintering, a fine- or coarse-grained green body, which was formed in a previous process step, for example by extrusion, becomes a solid workpiece. The sintered product only receives its final properties such as hardness, strength or thermal conductivity, which are required for the respective application, through the temperature treatment.
Adequate Systherms – furnaces for this treatment:
Sintering
Contact
SYSTHERMS GmbH
Gutenbergstrasse 3
D-97297 Waldbüttelbrunn
Phone: +49 (0) 931 35 94 30
Fax: +49 (0) 931 35 94 320
E-mail: Contactform
Overview
Quality & Reliability with SYSTHERMS
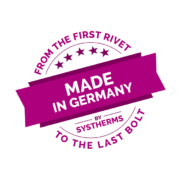